
Slot Die 코팅 공정의 모델 예측 제어를 위한 다중목적 최적화 기법
© 2021 KIIE
Abstract
In the field of chemical engineering, several studies proposed to find appropriate operating parameters of the Slot Die coating process, but there is still a problem with product quality because of limitation through trial and error by workers at the manufacturing site. Moreover, PID (Proportional-Integral-Derivative) controller and MPC (Model Predictive Control) are mostly used as process control techniques but they still have some limitations such as nonlinearity, different environmental condition, complexity of response, or multiple objectives of manufacturing processes. In this paper, we propose a novel multiple objective model predictive control technique called MOORA (Multiple Objective Optimization based Regression Analysis) in the Slot Die coating process with multiple-input and multiple-output. In this study, modeling with multiple regression analysis, we derive input values and output target values. Furthermore, in the multiple objective optimization problem that find the best solution, the proposed method has shown better execution time and performance than NSGA-Ⅱ(Non-dominated Sorting Genetic Algorithm).
Keywords:
Slot Die Coating Process, Model Predictive Control, Multiple Objective Optimization1. 서 론
궁극적인 스마트 팩토리의 구축을 위해서는 제조 기술의 고도화뿐만 아니라 데이터에 기반을 둔 디지털 기술의 고도화가 병행되어야 한다. 또한, 제조 공정에 있어서 머신러닝 기술을 활용한 진단/예측을 넘어, 실제로 의사결정에 활용할 수 있도록 만드는 단계까지 요구되고 있는 상황이다(Shao et al., 2018).
특히, 실시간 의사결정의 자동화 단계가 필요한 부분은 공정제어의 영역이다. 광의의 공정제어는 공정의 출력변수(피제어변수)를 원하는 상태로 유지하기 위한 전반적인 조작을 의미한다. 기본적인 공정제어는 공정의 물리적 특성을 모사하는 미분방정식으로부터 출발하여, 미분방정식의 라플라스 변환 형태로 표현되는 전달함수(Transfer Function)를 통해 공정의 동특성을 나타내고 이를 기반으로 제어시스템을 구축하는 것이 일반적이다(Seborg et al., 1986).
공정의 출력변수와 설정값(목표값)을 비교하여, 그 차이를 기반으로 적절한 판단과 조작을 취함으로써 입력변수(조절변수)를 수정하는 방식을 되먹임 제어(Feedback Control)라고 하며, 오차와 조작량이 연속적인 경우를 연속제어(Continuous Control) 라고 한다(Smith et al., 2005).
이러한 연속제어를 위한 대표적인 방법으로는 PID(Proportional-Integral-Derivative) 제어기와 MPC(Model Predictive Control)가 있다. PID 제어기는 출력값과 설정값을 비교하여 구한 오차값을 이용하여 제어값을 계산하는 구조를 가지고 있다. PID 제어기는 구조가 간단하고 제어 성능이 우수하기 때문에 산업현장에서 많이 쓰이고 있지만, 공정의 모델링 시간이 오래 걸리고 조업자의 주관이 많은 영향을 미치는 문제가 있다(Sung et al., 1996). 그리고 PID 제어기는 현대 공정의 다양한 시스템과 비선형적인 요인으로 인해 파라미터 조율의 어려움이 있으며(Zhou et al., 2013), MIMO(Multiple Input Multiple Output) 공정에서 변수 간 상호작용으로 인해 PID 제어기를 활용하기 어려운 것 또한 현실적인 문제이다(Unar et al., 1995). 이와 달리 일반적인 MPC는 대상공정의 여러 물리/화학적인 법칙과 실 운전 자료에 기초한 수학적 모델을 기반으로 함으로써, PID 제어기보다 정확하고 안정된 제어 응답을 얻을 수 있다(Seo et al., 2002). 하지만 MPC는 최적화 과정 중 최종값에 수렴하기까지 걸리는 연산시간을 예측하기 어렵기 때문에, 실시간성이 요구되는 제어기법에 적용되기 어려운 한계가 존재한다(Lee et al., 2020).
최근 현대 공정이 가지고 있는 비선형성, 다양한 환경요인, 응답특성의 복잡도, 다중목적함수 등의 문제를 머신러닝 기법과 다양한 최적화 기법을 응용하여 풀려는 시도가 확대되고 있다(Deyi et al., 2017; Kang et al., 2016; Lee et al., 2017; Lee., 2018; Smarra et al., 2018). 특히 다중목적함수를 가지는 문제에서는 상충하는 목적함수들을 동시에 최적화하기 위해 우선 가능한 해 집단을 찾아야 한다. 다시 말해서 목적함수들이 가지는 실현 가능한 영역에서 최적의 해를 가지는 후보들을 의미하는 <Figure 1>의 Pareto-optimal front를 구하고 적절한 후보를 선택해야 한다(Deb, 2018). 하지만 위 방법은 최적해 후보를 구하고 선택하는 과정을 반복해야 하기 때문에 실시간성이 요구되는 공정제어 영역에 적용하기에 어려움이 있다.
본 논문에서는 기존의 PID 제어기와 MPC가 가지는 한계를 극복하고, 다중목적함수 최적화가 필요한 공정의 연속제어를 위해 다중회귀분석을 이용한 순차적 모델링과 제어변수의 최적 제어값을 산출하는 데이터 기반 모델 예측 제어 방법인 MOORA(Multiple Objective Optimization based Regression Analysis)를 제안한다.
본 논문의 구성은 다음과 같다. 제 2장에서는 이차전지의 제조 공정 중 Slot Die 코팅 공정의 특징과 문제, 그리고 대표적인 코팅 공정 내의 제어 문제를 소개한다. 제 3장은 제안하는 방법론 설명과 의미에 대해 제시한다. 제 4장은 제안방법의 최적화 식과 NSGA-II 알고리즘과의 비교 및 성능 검증 결과를 서술한다. 마지막으로 제 5장에서 본 연구의 결론과 향후 연구 방향을 제시한다.
2. 연구 동기
이차전지의 제조과정 중 극판(Pole-plate)을 생산하는 공정은 <Figure 2>에서 보는 바와 같이 양극/음극재, 도전재, 바인더 등을 용매와 함께 섞은 슬러리를 알루미늄 혹은 구리 박막 위에 도포하는 코팅 공정과 도포된 슬러리의 용매를 건조시키는 건조 공정으로 구성된다. 건조가 완료된 극판은 압연 과정을 거친 뒤 조립 공정에 적합한 크기로 절단하는 슬리팅 과정을 거친다. 이후 양극, 분리막, 음극을 겹치고 말아서 Roll 형태를 만들고 이를 캔 또는 파우치의 형태에 담아 전해액을 주입하는 조립 공정을 거친 뒤에 충/방전의 반복을 통한 활성화 과정을 거쳐 최종 제품이 생산되게 된다(Nam, 2010).
ESS(Energy Storage System)나 EV(Electric Vehicle)용 배터리들은 여러 개의 배터리 셀(Cell)들을 직/병렬로 연결한 형태인 배터리 팩(Pack)의 형태로 구성되는데, 각 배터리 셀들의 품질이 일정하지 않은 경우 배터리의 내구성과 안정성에 큰 손상이 발생된다. 특히 각 배터리 셀의 품질은 코팅 공정의 품질에 좌우되고 있으며, 코팅 공정의 품질 중 슬러리의 균일한 도포에 의해 결정된다(Lyu et al., 2019).
일반적으로 코팅 공정은 고체 위의 기체를 액체로 치환하는 공정을 의미한다. 고체 위에 도포되는 코팅액은 용액이나 현탁액 그리고 고분자 용융체와 같이 복잡한 구조 및 구성의 물질들로 이루어진 경우가 대부분이다. 다양한 코팅 공정 중에 Slot Die 코팅 공정은 높은 정밀도와 빠른 생산속도로 인해 디스플레이나 이차전지 산업 등에서 많이 사용되고 있다. 특히 Slot Die 코팅 공정은 전계량(Pre-metered) 공정의 하나로 도포되는 지지체의 속도와 코팅 두께를 설정하면 물질 수지식에 의해 공급되는 코팅액의 양이 결정되는 시스템으로 코팅액의 물성과 관계없이 코팅 두께를 결정할 수 있다고 알려져 있으나 실제로는 코팅액의 유변물성, 점성, 점탄성, 점탄가소성 등이 공정의 설계 및 운영조건에 많은 영향을 미치고 있다(Kim et al., 2005; Nam, 2010).
화학 공학 분야에서는 Slot Die 코팅 공정의 운전 파라미터들의 적절한 운전 범위를 찾고자 하는 연구가 진행되고 있으나, 최적의 운전 범위를 찾는 과정 일부는 여전히 미지의 영역으로 남아 있는 상태이다(Ding et al., 2016). 실제 현장에서도 Slot Die 코팅 공정의 제어는 작업자들의 반복되는 시행착오를 통해 이루어지고 있으며, 작업자의 숙련도에 따라 제품의 품질 편차가 발생하는 문제점을 안고 있다.
이차전지 극판 코팅 공정에서 통상의 품질 척도로 금속 박막 위에 도포된 슬러리의 양이 사용된다. 도포된 슬러리의 양은 공정의 진행방향 그리고 이와 수직인 폭 방향을 일정한 영역으로 분할하여 측정/수집되고 있으나, 운전 파라미터의 최적 범위를 결정하는 문제에는 다수의 Y값(품질 척도)의 평균을 취하는 등의 방법으로 단변량화 하여 접근하는 방식이 일반적이다. 하지만 이와 같은 방법은 극판의 폭 방향 분포의 특성을 제대로 반영하기는 어려운 것이 현실이다. 특히, <Figure 3>은 극판위에 도포된 슬러리의 질량값을 3차원으로 시각화한 것으로, <Figure 3>에서 도시된 Y값의 국소적인 패턴이나 장애에 대한 정보를 반영하지 못하여 도출한 운전 인자의 최적값이 왜곡될 가능성이 크다는 문제점이 있다.
<Figure 4(a)>, <Figure 4(b)>는 1차적으로 도포되는 슬러리의 양인 다수의 X(제어변수)와 최종적으로 건조된 슬러리의 양인 Y(출력변수)값의 상관관계를 상관계수 행렬(a)과 상관계수가 0.6 이상인 변수간의 연결(b)을 시각화한 것으로, 예를 들어 x1과 y11, y18이 강한 양의 상관관계를 갖고 x2와 y18, y19가 강한 양의 상관관계를 가지는 등, 특정 제어변수는 특정 출력변수와 강한 상관관계를 가지는 것을 알 수 있다. 따라서 이를 고려하여 국소적 패턴과 시간에 대한 변동성(Time-varying Property), 국소적으로 발생하는 장애 등에 대한 Feedback Control을 위한 즉각적이고 연속적으로 수행 가능한 방법의 개발이 요구되는 상황이다.
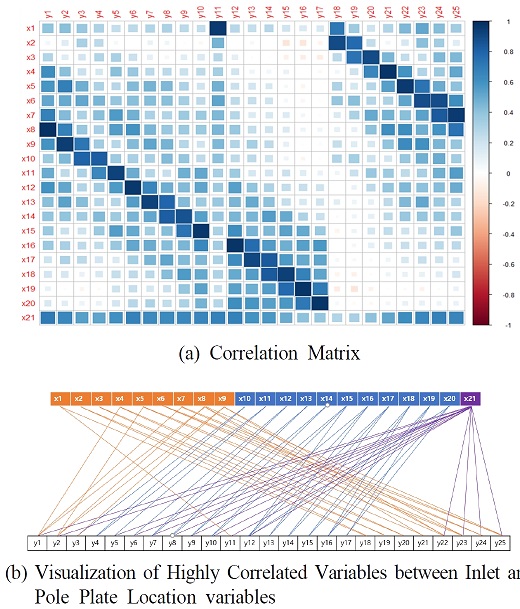
Representation of Correlation Coefficient between Input and Output Variables in Coating Process Data
일반적인 다중목적함수의 최적화 식은 식 (1)과 같다(Andersson, 2000).
(1) |
여기서 는 k개의 목적함수를 의미하며 x는 변수 공간 S의 부분집합이다. 이러한 다중목적함수 최적화 문제를 해결하기 위해 자연현상을 모방한 메타휴리스틱이 유용하게 활용되고 있다. 메타휴리스틱이란 자연현상을 관찰 및 모방하여 반복적으로 해를 개선 시키는 방법으로, 다중목적함수 최적화가 필요한 공정제어 영역에서는 동물 군집의 이동현상을 모방한 알고리즘인 PSO(Particle Swarm Optimization)를 이용하여 발전소를 제어하는 연구(Heo et al., 2006), PID 제어기 파라미터를 조율하기 위해 다목적유전알고리즘인 NSGA-Ⅱ를 활용한 연구(Ayala et al., 2012), 중력의 법칙을 이용하여 최적해를 구하는 GSA(Gravitational Search Algorithm)를 활용한 모바일 로봇의 경로추종 제어 연구(Merabti et al., 2014) 등이 있다. 특히, 다중목적함수를 최적화하기 위한 기법으로 NSGA-Ⅱ(Non-dominated Sorting Genetic Algorithm)가 대표적으로 활용되고 있다(Xiao et al., 2011). NSGA-Ⅱ는 유전알고리즘을 기반으로 하여 다중목적함수의 최적해들을 구하는 알고리즘으로, 예를 들어 <Figure 5>에서 보이는 해 A와 C의 관계에서 A의 목적함수들의 값이 모두 C보다 우월하면 A를 비지배해(Non-dominated Solution)라고 하며 이러한 비지배해들이 존재하는 Pareto-optimal front를 찾는다. NSGA-Ⅱ는 염색체들을 평가하는 방법으로 비지배해들에 순위를 부여하는 비지배 분류(Non-dominated Sorting)를 이용한다. 또한, 다양한 해들을 갖게 하기 위해서 각 개체들의 과밀거리(Crowding Distance)를 계산하여 동일한 순위에 속하는 개체 중 거리가 큰 개체를 다음 부모 개체군으로 선택한다. NSGA-Ⅱ의 기본 순서는 <Figure 6>과 같다. 먼저 무작위로 N 규모의 초기 개체군을 생성하고 유전알고리즘의 기본조작인 선택(Selection), 교차(Crossover), 변이(Mutation)를 통해 자손 개체군을 생성한다. 이후 부모 개체군과 자손 개체군을 합치고 비지배 분류와 동시에 각 개체의 과밀거리를 계산하고 비지배 순위와 과밀거리를 근거하여 새로운 부모 개체군을 만든다. 마지막으로 종료 조건에 만족할 때까지 위 과정을 반복한다(Liu et al., 2019).
3. Multiple Objective Optimization based Regression Analysis
모델 예측 제어를 위한 본 연구에서 제시하는 방법론의 순서는 <Figure 7>과 같다. 우선 다수의 제어변수와 상응하는 다수의 출력변수의 관계를 모델링함에 있어서, 학습 크기를 의미하는Window Size(N)과 이동 크기인 Step Size(T)를 설정하여 학습데이터(Training Data)에서 데이터를 추출한 후, 다중선형회귀모델을 학습시킨다. 예를 들어, N이 4000이고 T가 100이라면 i = 0일 때 1번째 데이터부터 4000번째의 데이터까지를 학습한다. i = 1일 때는 101번째 데이터부터 4100번째 데이터까지를 학습하는 순으로 진행된다. 모델을 학습시킨 후에는 학습된 모델의 가중치 행렬을 통해 최적 제어값을 산출한 후, 다음 T 시점 동안 공정을 제어한다. T시점이 지나면 i+1을 통해 Window를 이동시켜 순차적인 모델링과 최적 제어값을 산출할 수 있다. 만약 학습데이터의 크기(Training Data Size)가 N+T*i보다 작으면 학습데이터에서 추출할 수 있는 데이터가 N보다 작기 때문에 알고리즘이 종료된다.
3.1 모델링
다중선형회귀모델은 제어변수와 출력변수의 상관관계를 통해 회귀계수를 도출하기 때문에 출력변수에 대한 제어변수들의 영향력을 알 수 있다(Zou et al., 2003). 다수의 출력변수와 제어변수를 가지는 모델에서는 각 출력변수에 대한 회귀모델을 구축하여 제어변수들이 각 출력변수에 미치는 영향(회귀계수)을 알 수 있다.
X = (X1, ⋯, Xm)로 Y = (Y1, ⋯, Yd)를 예측하기 위한 다중선형회귀모델 구축 시, 가중치 행렬 를 구하기 위한 목적함수는 식 (2)와 같다(Borchani et al., 2015).
(2) |
여기서 l은 데이터의 인덱스를 나타내고 각 y에 대한 최소제곱법을 통해 d×m 가중치 행렬을 구할 수 있다. 이를 정규 방정식으로 표현하면 식 (3)과 같다.
(3) |
여기서 X는 m개의 제어변수와 n개의 데이터 수를 의미하는 m×n 행렬, Y는 d개의 출력변수와 n개의 데이터 수를 가지는 d×n 행렬로 식 (4)를 통해 d×m 가중치 행렬 를 구할 수 있다.
(4) |
식 (3)에서 양변에 XT를 곱하여 정방행렬(Square Matrix) XXT를 만든 뒤, 양변에 XXT의 역행렬을 곱하여 가중치 행렬 를 구한 것이다. 가중치 행렬 의 의미는 다수의 제어변수 X가 각 출력변수 y에 대한 영향력을 의미한다. 예들 들어 첫 번째 행의 m개의 성분은 첫 번째 출력변수에 대한 X의 가중치이다.
3.2 최적 제어값 도출
식 (2)에서 구한 를 통해 타겟 를 산출하는 xj를 구하는 목적함수는 식 (5)와 같다.
(5) |
여기서 Target 는 사용자가 직접 설정해야 하며 다음 식 (6)을 통해 최적 제어값을 얻을 수 있다.
(6) |
식 (4)에서 주어진 Y와 X를 통해 을 구했다면 식 (6)에서는 설정한 와 앞에서 구한 을 통해 를 구하는 과정으로 양변에 βT를 곱하여 정방행렬 βTβ로 만든 뒤 βTβ의 역행렬을 양변에 곱하여 최적 제어값 를 구할 수 있다.
본 논문에서 제안하는 방법은 위의 식들을 이용하여 주어진 공정 데이터에서 학습 Window를 이동시키며 순차적 모델링 및 최적해를 도출하는 과정을 일반화한 것이다. 제안방법의 특징은 다중회귀 분석을 통해 출력변수들에 해당하는 각 가중치들을 모두 구하고, 이를 이용하여 타겟값을 도출하는 제어변수들을 찾는 것이다. 특히 제안방법은 모델링 및 최적 제어값을 도출하는 과정의 연산 속도가 빠르고 별도의 제약조건이 필요하지 않기 때문에 실시간성이 요구되는 공정제어 영역에서 활용하기에 적절하다. 또한, 학습모델은 실시간으로 수집되는 데이터를 통해 업데이트되기 때문에 시간에 따른 공정의 변동성을 고려할 수 있는 장점이 있다.
4. 실험 및 결과
본 논문에서는 1차적으로 극판에 도포된 영역별 슬러리의 양을 나타내는 제어변수가 21개, 슬러리의 최종 두께를 나타내는 출력변수가 25개, 그리고 데이터의 개수가 4800개로 다수의 제어변수와 출력변수를 가지는 Slot Die 코팅 공정 데이터를 실험데이터로 활용하였다. Window Size와 Step Size에 따른 학습 모델의 성능지표로 출력변수의 평균 Test RMSE(Root Mean Squared Error)를 실험을 통해 <Table 1>에 나타내었으며, 본 연구에서는 Test RMSE가 가장 작은 Window Size = 4000, Step Size = 100으로 모델을 학습시켰다.
우선 제안방법의 첫 단계인 모델링을 위한 회귀모형은 식 (7)과 같다.
(7) |
여기서 l은 데이터의 인덱스를 나타내고 학습할 데이터는 1부터 4000까지 설정하였다. i는 출력변수의 수로 25개, j는 제어변수의 수로 21개를 설정하였다. 최소제곱법을 통해 각 모델의 가중치를 구하면 25×21 가중치 행렬인 을 구할 수 있다. 모델을 학습시킨 후, 본 논문에서 분석한 배터리 기종의 슬러리 도포량 목표값인 21.74로 Target 를 설정하여 제어변수 xj를 구하는 목적함수는 식 (8)과 같다.
(8) |
앞서 구한 가중치 행렬과 제어변수 xj를 곱하여 나온 값과 21.74와 차이의 제곱합이 최소가 되는 식으로 위 식을 통해 나온 최적의 제어값은 <Table 2>와 같다.
도출된 최적 제어값을 통해 Step size인 100만큼 제어를 진행한 후, 다시 학습 데이터를 101부터 4100까지 설정하여 모델을 학습시켜 최적 제어값을 구하고 제어하는 과정을 반복하는 것이 본 논문에서 제시하는 방법론이다. <Figure 8>은 학습한 모델을 통해 평가데이터(Test Set)를 예측하는 동시에 산출한 최적 제어값으로 제어한 후, Window를 Step Size만큼 이동시켜 순차적인 모델링 및 제어가 진행되는 과정을 도시한 것이다.
본 논문에서 제시하는 방법론의 성능과 NSGA-Ⅱ 알고리즘을 비교하기 위하여 최적 제어값을 도출하는 다중목적함수는 다음 식 (9)과 같다.
(9) |
본 논문에서는 실험데이터의 제어변수들이 모두 실수 21과 22 사이에 분포되어있기 때문에, 해 공간 탐색을 더 용이하게 하기 위해 제약조건으로 a = 21, b = 22로 설정 후, 앞서 구한 각 목적함수에 해당하는 가중치 ai와 21와 22 사이의 실수를 가지는 xj를 곱하여 나온 결과값이 21.74와의 차이가 최소화 되도록 하였다. NSGA-Ⅱ 알고리즘으로 다중 목적함수 최적화를 수행하였다. 하이퍼 파라미터인 개체군 수(Size of Population)는 100, 세대 수(Number of Generations)는 1000, 변이 확률(Mutation Probability)은 0.2로 하였고, 결과로 나온 최적해 후보 중 첫 번째 후보를 선택하였다. NSGA-Ⅱ 알고리즘으로 구한 최적의 제어값은 <Table 3>과 같다.
학습모델의 성능지표로는 평균제곱근오차(Root Mean Square Error, RMSE)를 사용하였으며, 다수의 출력변수를 가지는 모델의 성능을 확인하기 위해 RMSE의 평균값(Average Root Mean Squared Error, aRMSE)을 식 (10)을 통해 계산하였다(Borchani et al., 2015).
(10) |
여기서 yi는 실제 슬러리의 질량을 의미하며, 는 예측한 슬러리의 질량을 의미한다. aRMSE는 출력변수의 수인 d개의 yi와 의 차이의 제곱합을 데이터의 수 N으로 나눠준 값의 제곱근을 모두 합하여 평균을 구한 것이다.
<Table 4>는 에 대한 RMSE 평균을 구한 Train aRMSE, Test aRMSE로 Train aRMSE의 평균은 0.01379, Test aRMSE의 평균은 0.01371로 나타났다. 본 논문에서 분석한 배터리 기종의 슬러리 도포량 목표값인 21.74로 Target 를 설정하여 <Table 4>에서 학습한 각 모델에서 제안방법과 NSGA-Ⅱ로 구한 최적 제어값을 통해 예상되는 출력변수의 값을 시각화한 결과를 <Figure 9>에 도시하였다. 본 논문의 제안방법을 통해 구한 예상 출력변수의 값은 21.74 근처에 모여 있는 반면에, NSGA-Ⅱ는 제안방법보다 21.74와의 거리가 멀고, 예상 출력변수를 구한 시점마다 일정하지 않은 결과가 나타났으며, 분산 또한 불안정한 것을 볼 수 있다. <Table 5>는 <Figure 9>를 표로 나타낸 것으로 제안방법을 통해 나온 최적 제어값으로 구한 의 평균은 모든 T 시점에서 21.74이지만, NSGA-Ⅱ는 평균이 21.69로 나타났으며 의 분산도 제안방법보다 큰 것으로 나타났다. <Table 6>을 보면 최적해를 구하는 실행시간 또한 제안방법이 적게 나타남을 확인하였다. 이는 제안방법인 MOORA의 경우, 미리 구한 가중치 행렬을 통해 별도의 제약조건 없이 최적 제어값을 구하였기 때문에 일관된 결과를 나타내었지만, NSGA-Ⅱ는 하나의 최적해가 아닌 여러 최적해 후보를 구하기 때문에 그 중에서 선택해야 하며, 목적함수의 수가 25개로 최적해를 찾기에는 그 수가 많아 일정하지 않은 결과가 나타난 것으로 보인다.
<Figure 10>은 극판 위에 도포된 기존의 슬러리와 제안방법을 통해 얻은 예상되는 슬러리를 나타낸 것으로 x축은 극판의 특정 위치를 나타내며 y축은 슬러리의 질량값을 의미한다. 그림을 통해 분산이 크고 균일하지 않았던 기존 슬러리에 비해 제안방법의 결과가 목표값인 21.74에 가까우면서 분산이 최소화된 것을 알 수 있다.
5. 결론 및 향후 연구
본 논문에서는 이차전지 극판 코팅 공정에서 지금까지는 작업자의 수작업으로 이루어졌던 Slot Die 코팅 공정을 자동적으로 제어하기 위한 방법론으로 다수의 제어변수와 다수의 출력변수에 대한 다중선형회귀 순차적 모델링과 최적화 식을 이용한 데이터 기반 모델 예측 제어 기법을 제시하였다. 특히, 모델링 과정에서 다중선형회귀식을 이용하여 예측된 의 평균 RMSE를 통해 예측성능을 확인하였고, 다중목적함수를 가지는 상황에서 제안방법의 최적화 과정이 NSGA-Ⅱ보다 짧은 연산시간과 높은 정확도를 가지는 것을 확인하였다. 이는 실시간성을 요구하는 공정제어의 영역에서 의미 있는 결과라고 볼 수 있다.
다수의 출력변수를 평균을 취하여 단변량화 하면 타겟값에 근사시키는 최적의 제어값을 찾는다고 하더라도 평균이라는 하나의 값이기 때문에 각 출력변수는 균일한 분포를 갖지 못하게 된다. 따라서 본 논문에서 제시하는 모든 출력변수를 모델링 하는 방법이 슬러리 양의 예측에는 더 효율적이지만, 실제 배터리 공정에서 극판 위에 도포된 슬러리의 물리적 분포 특성을 온전히 반영하지 못하는 점은 본 연구의 한계점이라고 할 수 있다. 향후 연구에서는 다수의 출력변수가 서로 상관관계를 가지는 공정에서 예측의 정확도와, 출력변수들이 가지는 물리적으로 자연스러운 분포를 고려한 모델링 및 최적화 방법을 수학적 기법과 머신러닝을 활용하여 연구하고, 이를 통해 더 강건한 모델 예측 제어에 기여 하고자 한다.
Acknowledgments
이 논문은 2020년도 정부(교육부)의 재원으로 한국연구재단의 지원을 받아 수행된 기초연구사업임(No. NRF-2020R1F1A1074947).
References
- Andersson, J. (2000), A Survey of Multiobjective Optimization in Engineering Design, Department of Mechanical Engineering, Linktjping University, Sweden.
-
Ayala, H. V. H. and dos Santos Coelho, L. (2012), Tuning of PID Controller based on a Multiobjective Genetic Algorithm Applied to a Robotic Manipulator, Expert Systems with Applications, 39(10), 8968-8974.
[https://doi.org/10.1016/j.eswa.2012.02.027]
-
Borchani, H., Varando, G., Bielza, C., and Larranaga, P. (2015), A Survey on Multi Output Regression, WIREs Data Mining and Knowledge Discovery, 5(5), 216-233.
[https://doi.org/10.1002/widm.1157]
-
Merabti, H. and Belarbi, K. (2014), Multi-Objective Predictive Control : A Solution Using Metaheuristics, International Journal of Computer Science & Information Technology, 6(6), 147.
[https://doi.org/10.5121/ijcsit.2014.6612]
-
Deb, K. (1999), Multi-Objective Genetic Algorithms : Problem Difficulties and Construction of Test Problems, Evolutionary Computation, 7(3), 205-230.
[https://doi.org/10.1162/evco.1999.7.3.205]
-
Ding, X., Liu, J., and Harris, T. A. (2016), A Review of the Operating Limits in Slot Die Coating Processes, AIChE Journal, 62(7), 2508-2524.
[https://doi.org/10.1002/aic.15268]
-
Deyi, M. and Xiaoqian, Z. (2017), Stochastic Programming for the Optimization of Transportation-Inventory Strategy, Industrial Engineering and Management Systems, 16(1), 44-51.
[https://doi.org/10.7232/iems.2017.16.1.044]
-
Heo, J. S., Lee, K. Y., and Garduno-Ramirez, R. (2006), Multiobjective Control of Power Plants Using Particle Swarm Optimization Techniques, IEEE Transactions on Energy Conversion, 21(2), 552-561.
[https://doi.org/10.1109/TEC.2005.858078]
-
Kang, S. H. and Kim, S. B. (2016), Multivariate Monitoring of the Metal Frame Process in Mobile Device Manufacturing, Journal of Korean Institute of Industrial Engineers, 42(6), 395-403.
[https://doi.org/10.7232/JKIIE.2016.42.6.395]
- Kim, S. Y. and Jung, H. U. (2005), Slot Die Coating Processes, News & Information for Chemical Engineers, 23(5), 524-529.
-
Lyu, C., Song, Y., Wang, L., Li, J., Zhang, B., and Liu, E. (2019), A New Method for Lithium-ion Battery Uniformity Sorting based on Internal Criteria, Journal of Energy Storage, 25, 100885
[https://doi.org/10.1016/j.est.2019.100885]
-
Lee, T. G. and Kang, Y. S. (2020), Development of Deep Artificial Neural Network Controller Based on Non-linear Model Predictive Control Data for Real-time Autonomous Driving, Institute of Control, Robotics and Systems, 26(5), 302-311
[https://doi.org/10.5302/J.ICROS.2020.20.0013]
- Lee, Y. H. (2018), PSO-Based PID Controller for AVR Systems Concerned with Design Specification, Journal of the Korea Academia-Industrial Cooperation Society, 19(10), 330-338.
-
Lee, D. H., Kim, B. R., Yang, J. K., and Oh, S. H. (2017), Dual Response Surface Optimization using Multiple Objective Genetic Algorithms, Journal of Korean Institute of Industrial Engineers, 43(3), 164-175.
[https://doi.org/10.7232/JKIIE.2017.43.3.164]
-
Liu, W., Liu, C., Lin, Y., Bai, K., Ma, L., and Chen, W. (2019), Multi-objective Optimal Scheduling Method for a Grid-Connected Redundant Residential Microgrid, Processes, 7(5), 296.
[https://doi.org/10.3390/pr7050296]
- Nam, J. W. (2010), Continuous Liquid Coating Process and Future Tasks, News & Information for Chemical Engineers, 28(5), 552-562.
-
Pedersen, G. K. and Yang, Z. (2006), Multi-Objective PID-Controller Tuning for a Magnetic Levitation System Using NSGA-II, In Proceedings of the 8th Annual Conference on Genetic and Evolutionary Computation, 1737-1744.
[https://doi.org/10.1145/1143997.1144280]
-
Shao, G., Brodsky, A., and Miller, R. (2018), Modeling and Optimization of Manufacturing Process Performance using Modelica Graphical Representation and Process Analytics Formalism, Journal of Intelligent Manufacturing, 29(6), 1287-1301.
[https://doi.org/10.1007/s10845-015-1178-6]
- Seo, J. W., Kim, K. H., Kim, S. J., Oh, M., and Lee, T. H. (2002), Control of Atmospheric Distillation Unit Using Model Predictive Control Technique, Korean Chemical Engineering Research, 40(2), 152-158.
- Smith, C. A. and Corripio, A. B. (2005), Principles and Practices of Automatic Process Control, John Wiley &Sons.
-
Smarra, F., Jain, A., de Rubeis, T., Ambrosini, D., D’Innocenzo, A., and Mangharam, R. (2018), Data-Driven Model Predictive Control Using Random Forests for Building Energy Optimization and Climate Control, Applied Energy, 226, 1252-1272.
[https://doi.org/10.1016/j.apenergy.2018.02.126]
- Sung, S. H. and Han, C. H. (1996), A Method for Auto-Tuning of PID in a Chemical Process, Institute of Control, Robotics and Systems, 2(1), 72-84
-
Seborg, D. E., Edgar, T. F., and Shah, S. L. (1986), Adaptive Control Strategies for Process Control : A Survey, AIChE Journal, 32(6), 881-913.
[https://doi.org/10.1002/aic.690320602]
- Unar, M. A., Murray-Smith, D. J., and Shah, S. A. (1995), Design and Tuning of Fixed Structure PID Controllers-a Survey(Doctoral dissertation, University of Glasgow, Glasgow, Scotland, UK).
- Xiao, X. W., Xiao, D., Lin, J. G., and Xiao, Y. F. (2011), Overview on Multi-Objective Optimization Problem Research, Application Research of Computers, 3, 001.
-
Zhou, Y. T., Nie, J. B., Han, N., Chen, C., and Yue, Z. F. (2013), Study on PID Parameters Tuning based on Particle Swarm Optimization, In Advanced Materials Research, 823, 432-438.
[https://doi.org/10.4028/www.scientific.net/AMR.823.432]
-
Zou, K. H., Tuncali, K., and Silverman, S. G. (2003), Correlation and Simple Linear Regression, Radiology, 227(3), 617-628.
[https://doi.org/10.1148/radiol.2273011499]
김용민 : 한국산업기술대학교 산업경영학과에서 2020년 학사학위를 취득하고 한국산업기술대학교에서 스마트팩토리융합학과 석사과정에 재학 중이다. 연구분야는 최적화, 데이터마이닝이다.
이규종 : 고려대학교 산업경영공학과에서 2011년 학사, 2013년 석사학위를 취득하고 2019년까지 LG화학 연구소 책임 연구원으로 근무하였으며, 현재는 삼성SDS 데이터분석그룹 책임 컨설턴트로 재직하고 있다. 연구분야는 머신러닝 및 공정제어이다.
주민식 : 1998년 학사, 2000년 석사, 2006년 박사학위를 한양대학교 기계설계학과에서 취득하고 2008년부터 지금까지 데이터분석 수석컨설턴트로 재직중이다. 연구분야는 수치최적화 이론을 이용한 능동학습 및 전이학습을 활용한 제조데이터 분석기법의 개발과 적용이다.
강지훈 : 2009년 광운대학교 경영학부에서 학사학위를 취득 후, 고려대학교 산업경영공학과에서 2011년 석사학위를, 2015년 박사학위를 취득하고 2019년까지 삼성 SDS 데이터분석그룹 Senior Engineer로 근무하였다. 현재는 한국산업기술대학교 경영학부 조교수로 재직하고 있다. 대표 연구분야로는 물리모델과 머신러닝의 결합 기법, 최적화 및 최적제어, 품질 및 예지보전 등이 있다.